How Listening to Workers Makes Risk Assessments Smarter
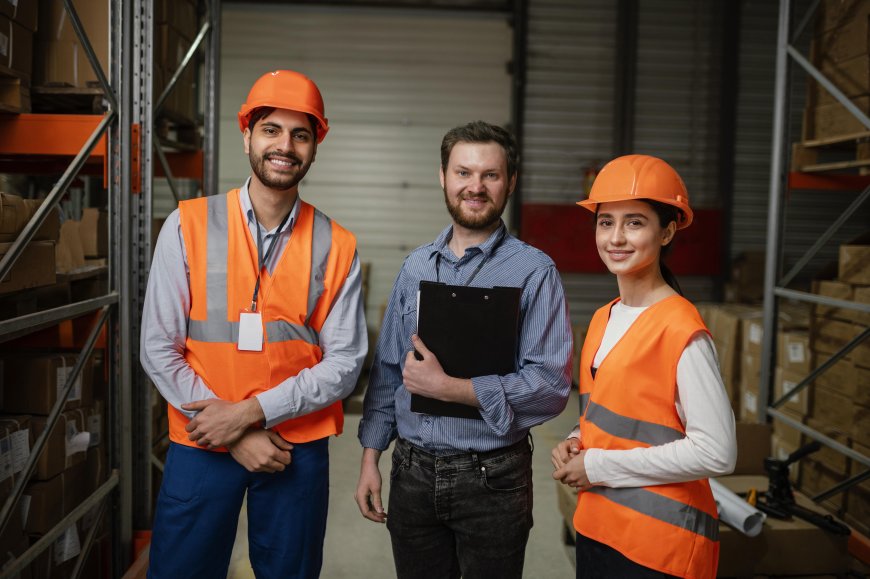
In many workplaces, risk assessments are treated like a checklist—a formality completed behind closed doors by managers or safety officers. But the truth is, the smartest and most effective risk assessments are those that involve the people who actually face the risks every day: the workers. Listening to workers not only helps uncover hidden dangers but also creates a culture where safety is everyone's job.
When we ignore the voices of our team members, we miss out on valuable insights that could prevent injuries, accidents, and even fatalities. Instead, when we include workers in the process, we create safer environments and smarter solutions.
Why Workers Know Best
Imagine you're managing a warehouse. You’ve walked through the space, followed the checklist, and marked it “safe.” But Ahmed, a forklift operator, has been navigating tight corners daily and knows exactly which area lacks proper lighting and increases the chances of a collision.
That’s where listening to workers makes risk assessments smarter. Workers understand the details of their tasks better than anyone else. They experience the conditions first-hand and often see the hazards that go unnoticed by supervisors or external auditors.
Read more about NEBOSH course fees in Pakistan and how understanding risk assessments through formal training can elevate your role in safety management.
Step-by-Step: How to Involve Workers in Risk Assessments
Step 1: Start with a Simple Conversation
You don’t need a fancy form to start. Pull your workers into a quick, informal discussion. Ask open-ended questions like:
-
“What part of your job feels risky?”
-
“Have you ever had a close call? What happened?”
-
“Is there any equipment or area you avoid?”
These casual conversations build trust and open the door to more detailed insights.
Step 2: Observe Together
Bring workers along during walk-through inspections. Let them point out issues and explain the tasks they’re performing. For example, a chemical plant worker might reveal that a valve leaks slightly during nighttime shifts—something supervisors never see.
Step 3: Document Their Observations
Create a simple log where workers can report hazards anonymously if they prefer. Encourage them to include suggestions, not just complaints. Often, they already know how to fix the problem but just haven’t been asked.
Step 4: Include Them in Decision-Making
When it comes time to decide on control measures or safety solutions, invite a few workers to be part of the discussion. Their insights can guide better decisions, and their involvement boosts compliance—because they helped shape the solution.
Step 5: Follow Up
Always go back to your team with updates. Let them know what changes are happening based on their input. This step builds confidence and shows that their voice matters.
Anecdote: A Factory Turned Safer Through Listening
At a textile factory in Lahore, managers noticed frequent complaints about back pain. They brought in ergonomic chairs and redesigned the workstations—but the complaints kept coming.
Finally, they invited a few workers to share their day-to-day experience. One seamstress explained that the breaks were too short and the pace of work too fast. The solution? Adjust the work rotation schedule and allow for short stretching breaks. Within a month, injury reports dropped by 40%.
This real change didn’t come from an expensive consultant or high-tech equipment. It came from listening to workers.
The Hidden Hazards Only Workers Know
Many workplace hazards don’t fit neatly into boxes. They're not just about open wires or slippery floors. They include:
-
Repetitive tasks that cause strain
-
Noise pollution that leads to fatigue
-
Unwritten practices, like skipping safety steps to meet deadlines
These are the kinds of issues that rarely show up on risk assessment forms—but they’re well known to workers.
Benefits of Worker Involvement
-
Smarter hazard identification: You’ll find the issues that actually matter.
-
Better compliance: When workers help design the rules, they’re more likely to follow them.
-
Stronger safety culture: People feel respected and involved.
-
Lower injury rates: Real risks are addressed in practical ways.
How This Applies Across Different Industries
In Construction
Construction workers often skip using safety harnesses because the attachment points are too far away. By listening, safety officers can redesign fall protection systems to make them more user-friendly.
In Healthcare
Nurses often lift patients manually because lifts are unavailable or inconvenient. Their feedback can lead to better policies and equipment placement.
In Manufacturing
Workers might bypass lockout/tagout procedures during equipment repairs to save time. Understanding why can lead to changes that improve compliance without slowing down productivity.
Overcoming Common Obstacles
Some employers hesitate to involve workers, thinking:
-
“They won’t take it seriously.”
-
“They don’t know enough about safety.”
But experience shows the opposite. Workers care deeply about their own safety—and their coworkers'. They just need an opportunity to be heard.
How to Encourage Honest Input
-
Create safe spaces for speaking up.
-
Reward openness, not silence.
-
Act on what you hear—nothing shuts people down faster than being ignored.
Tools and Tips for Better Listening
-
Use anonymous suggestion boxes for shy team members.
-
Hold regular toolbox talks and ask one question at the end.
-
Include a “hazard of the week” discussion in team meetings.
-
Rotate worker representatives on safety committees.
These small steps lead to big changes.
What Happens When You Don’t Listen
Ignoring workers can lead to:
-
Undetected hazards
-
Increased injury claims
-
Low morale
-
Distrust in safety programs
One company had a machine that frequently jammed. Workers knew how to fix it, but the process was unsafe. Management ignored the warnings—until one day, a worker was seriously injured. The tragedy could’ve been prevented with a simple conversation.
Explore the full details on NEBOSH course duration and fees in Pakistan to understand your options better.
Listening Isn’t Optional—It’s Essential
Risk assessments can’t be done from behind a desk. They need ears on the ground. Workers are not just laborers; they are the eyes, ears, and early warning system of any workplace.
Listening to them is not only smart—it’s the key to a safer, healthier, and more productive environment.
Final Thoughts: Smart Safety Starts with Listening
When workers speak, they do more than complain—they offer insight. Smart managers understand this. They use risk assessments not as a formality, but as a living, breathing part of the workplace culture.
So the next time you walk the floor, start with a question, not a checklist. Ask: “What do you see that I don’t?”
The answers might just save a life.