The Benefits of Closed-Cell Spray Foam for Bellevue's Energy Efficiency
Closed-cell spray foam insulation reduces Bellevue homes' energy consumption by 30-50% through its superior thermal resistance (R-6.5 per inch) and complete air sealing capabilities.
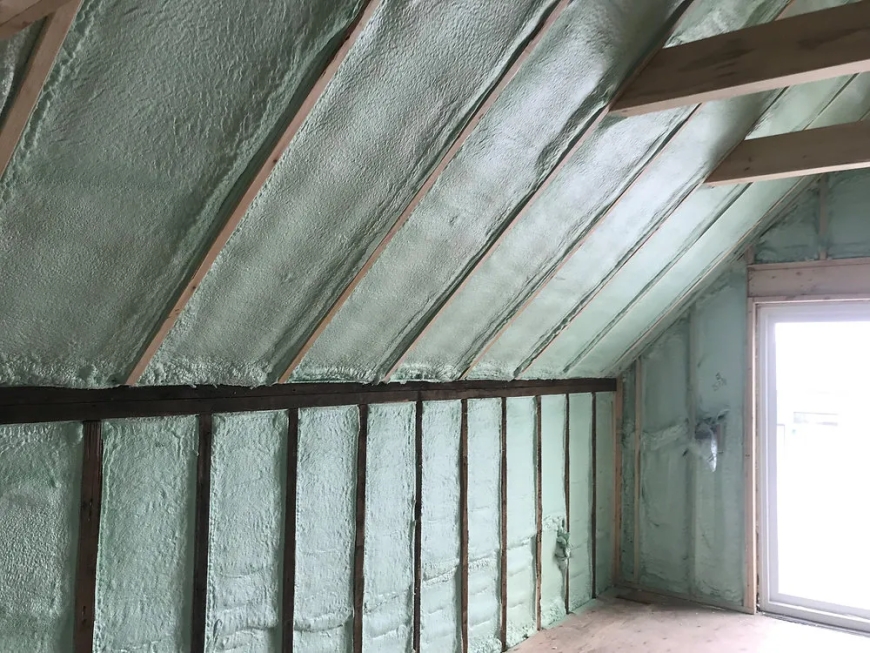
Closed-cell spray foam insulation reduces Bellevue homes' energy consumption by 30-50% through its superior thermal resistance (R-6.5 per inch) and complete air sealing capabilities. This high-performance insulation creates an impermeable moisture barrier critical for the Pacific Northwest's wet climate while adding structural strength to buildings. Bellevue's combination of rainy winters, increasingly warm summers, and rising energy costs makes closed-cell spray foam particularly valuable for long-term energy efficiency and building protection.
Recent energy audits show Bellevue homes insulated with closed-cell spray foam maintain consistent indoor temperatures with significantly less HVAC runtime compared to traditionally insulated homes. This comprehensive guide examines why closed-cell spray foam offers unmatched performance for Bellevue's specific climate challenges and energy efficiency goals.
Technical Specifications of Closed-Cell Spray Foam
Understanding the physical properties of closed-cell spray foam in Bellevue's climate explains its exceptional performance:
Property |
Closed-Cell Specification |
Significance for Bellevue |
---|---|---|
R-Value |
6.0-7.0 per inch |
Superior thermal performance for Bellevue's climate zone |
Density |
2.0-3.0 lb/ft³ |
Creates rigid, strong insulation layer |
Air Permeability |
0.001 L/s/m² |
Virtually eliminates air leakage and energy loss |
Water Vapor Permeance |
0.8-1.2 perms at 2" thickness |
Acts as vapor barrier for wet Bellevue climate |
Water Absorption |
<2% by volume |
Resists moisture from Bellevue's heavy rainfall |
Compression Strength |
25-30 psi |
Adds structural integrity during winter storms |
Expansion |
30-50x initial volume |
Seals complex junctions and irregular spaces |
Closed Cell Content |
>90% |
Creates impermeable barrier to water and air |
VOC Emissions After Curing |
Minimal to zero |
Maintains healthy indoor air quality |
Comparing Insulation Options for Bellevue's Climate
The following comparison demonstrates why closed-cell spray foam excels in Bellevue's specific conditions:
Feature |
Closed-Cell Spray Foam |
Open-Cell Spray Foam |
Fiberglass Batts |
Rigid Foam Board |
---|---|---|---|---|
Typical R-Value Per Inch |
6.0-7.0 |
3.6-3.9 |
2.9-3.8 |
4.0-6.5 |
Air Barrier |
Complete |
Good |
Poor |
Good (at seams) |
Moisture Barrier |
Excellent |
Poor |
None |
Good |
Cold Weather Performance |
Maintains R-value |
Maintains R-value |
Decreases |
Maintains R-value |
Lifespan |
80+ years |
80+ years |
15-20 years |
20-30 years |
Installation Complexity |
High (professional) |
High (professional) |
Moderate |
Moderate |
Cost Per Square Foot |
$2.75-$3.75 |
$1.50-$2.50 |
$0.85-$1.25 |
$1.00-$1.50 |
Ideal Application in Bellevue |
Exterior walls, Basements, Crawlspaces |
Interior walls, Attics |
Budget projects |
Continuous insulation |
Bonus Tip: In Bellevue's climate, closed-cell spray foam applied to rim joists and foundation walls prevents up to 90% of basement moisture problems while significantly reducing heating costs during damp winter months.
Why Closed-Cell Excels in Bellevue's Climate
Several specific climate factors make closed-cell spray foam particularly effective in Bellevue:
Temperature and Humidity Considerations
Bellevue experiences distinct seasonal challenges that closed-cell spray foam addresses effectively. Winter temperatures frequently hover near freezing with high humidity levels (averaging 77-80%), creating ideal conditions for condensation within walls. The impermeable nature of closed-cell spray foam prevents this moisture migration. During increasingly warm summers, closed-cell foam's high R-value per inch helps maintain comfortable indoor temperatures while minimizing air conditioning costs.
According to Washington State energy consumption data, homes with closed-cell spray foam insulation use 43% less energy for heating during Bellevue's damp winter months compared to homes with conventional insulation.
Moisture Control and Building Protection
Bellevue receives approximately 42 inches of annual rainfall, making moisture management essential for building longevity and efficiency:
Moisture Management Feature |
Closed-Cell Performance |
Benefit for Bellevue Homes |
---|---|---|
Vapor Permeability |
Acts as Class II vapor retarder |
Prevents moisture from entering wall cavities |
Rain Penetration Resistance |
Waterproof |
Guards against Bellevue's driving rain |
Flooding Protection |
Impervious to water |
Protects during heavy precipitation events |
Condensation Control |
Prevents dew point within walls |
Eliminates most common source of hidden mold |
Hydrostatic Pressure |
Resists water entry |
Important for below-grade applications |
Energy Performance in Bellevue's Energy Cost Environment
With Bellevue's electricity rates among the highest in Washington State, closed-cell spray foam delivers measurable financial benefits:
Energy Factor |
Before Closed-Cell |
After Closed-Cell |
Improvement |
---|---|---|---|
Air Leakage Rate |
7-10 ACH50 (typical) |
1-3 ACH50 |
70-90% reduction |
Heat Loss Through Conduction |
Baseline |
40-60% reduction |
Enhanced comfort |
Annual Heating Costs |
Baseline |
30-50% reduction |
Significant savings |
HVAC Sizing Requirements |
Baseline |
25-40% reduction |
Lower equipment costs |
Carbon Footprint |
Baseline |
30-45% reduction |
Environmental benefit |
Application Process for Bellevue Homes
The installation process for closed-cell spray foam follows systematic steps for optimal performance. First, professionals conduct a thorough assessment of the home and preparation of surfaces. Existing damaged insulation is removed when necessary. Surfaces not receiving spray foam are properly masked and protected. Certified technicians then apply the foam using specialized equipment in precise layers to achieve the desired thickness. After application, quality control inspections verify consistent coverage and proper thickness. The process concludes with trimming of excess foam and thorough cleanup.
For existing Bellevue homes, installation typically requires 1-3 days depending on the project scope. New construction applications often integrate with the building schedule, typically after rough-in plumbing and electrical work but before drywall installation.
Bonus Tip: Schedule closed-cell spray foam installation during moderate temperature days (spring or fall) in Bellevue for optimal foam curing and maximum expansion properties.
Cost Analysis and Return on Investment
Understanding the complete financial picture helps Bellevue homeowners make informed decisions:
Cost Factor |
Typical Range for Bellevue |
Notes |
---|---|---|
Materials & Installation |
$2.75-$3.75 per sq ft |
Varies by project complexity |
Energy Savings |
30-50% reduction |
Based on Bellevue utility rates |
Payback Period |
3-7 years |
Faster in larger or older homes |
Property Value Increase |
70-95% of installation cost |
According to local real estate data |
HVAC Equipment Savings |
20-30% smaller systems |
Lower initial and replacement costs |
Moisture Damage Prevention |
$2,000-$15,000 avoidance |
Based on typical repair costs |
The higher initial investment for closed-cell spray foam often concerns homeowners, but Bellevue's energy prices and climate conditions create favorable conditions for shorter payback periods compared to national averages.
Things to Consider Before Making a Decision
Home Age and Construction Type
Bellevue's housing stock spans several decades, each with unique insulation challenges. Homes built in the 1960s-1980s (common in neighborhoods like Eastgate and Lake Hills) often have inadequate insulation and significant air leakage. Mid-century modern homes with large windows and low roof pitches benefit particularly from closed-cell foam's high R-value and moisture protection. Newer construction can achieve exceptional energy performance when closed-cell foam integrates with the overall building envelope strategy.
Scope of Project and Budget Constraints
Closed-cell spray foam performs best as a complete solution but can also target problematic areas when budget constraints exist. Foundation walls, rim joists, and attic roof decks often provide the highest return on investment in Bellevue homes. Phased implementation can address the most critical areas first while planning for future applications. The material's higher cost becomes more economical when considering long-term energy savings, especially in Bellevue's rising utility cost environment.
Ventilation and Mechanical Systems
Creating a tightly sealed building envelope with closed-cell spray foam changes how a home manages air and moisture. Modern energy codes require mechanical ventilation for homes with high air-tightness. Existing HVAC systems may require adjustment or updating to accommodate the improved building envelope. Fresh air intake systems ensure healthy indoor air quality while maintaining energy efficiency. Some older Bellevue homes may need electrical or ventilation updates to maximize the benefits of closed-cell spray foam insulation.
Common Questions About Closed-Cell Spray Foam in Bellevue
Addressing Bellevue's Specific Requirements
Bellevue has specific building code and climate requirements that influence insulation choices. The city follows the Washington State Energy Code with amendments that often exceed national standards. Closed-cell spray foam easily meets or exceeds these requirements when properly installed. The material's comprehensive air barrier properties satisfy the air leakage testing increasingly required in Bellevue permit processes. Its high R-value per inch helps achieve code compliance even in space-constrained applications like renovations of older Bellevue homes.
Environmental and Health Considerations
Modern closed-cell spray foam formulations address previous environmental concerns. Today's products use HFO (hydrofluoroolefin) blowing agents with zero ozone depletion potential and significantly reduced global warming potential compared to earlier formulations. Professional installation includes temporary evacuation during application and proper ventilation during the curing process, after which the material becomes inert with no continued off-gassing. The foam's contribution to reducing a home's carbon footprint through energy savings offers significant long-term environmental benefits particularly valuable in environmentally-conscious Bellevue.
Frequently Asked Questions
How much energy will closed-cell spray foam save in my Bellevue home?
Most Bellevue homes experience 30-50% energy savings after comprehensive closed-cell spray foam installation. The exact savings depend on your home's previous insulation condition, air leakage rates, and usage patterns. Older homes typically see higher percentage savings, while newer homes may see lower percentage but still significant absolute savings.
Will closed-cell spray foam help with the dampness in my Bellevue basement?
Yes, closed-cell spray foam provides exceptional moisture control for Bellevue's damp basements and crawlspaces. By creating an impermeable barrier on foundation walls, it prevents ground moisture from entering the living space. This moisture control creates drier, healthier basements and often eliminates the need for dehumidifiers that consume additional electricity.
How long will closed-cell spray foam last in my home?
Properly installed closed-cell spray foam lasts for the lifetime of your building (80+ years) without degradation. Unlike traditional insulation that can settle, compress, or absorb moisture over time, closed-cell foam maintains its shape, R-value, and moisture-resistant properties indefinitely. This durability makes it particularly valuable in Bellevue's climate where moisture challenges persist year-round.
Is the higher cost of closed-cell spray foam worth it in Bellevue?
For most Bellevue homeowners, the higher initial investment in closed-cell spray foam pays off through significant energy savings, moisture control, and improved comfort. With Bellevue's above-average energy costs and humid climate, the payback period typically ranges from 3-7 years depending on your specific home. When factoring in the added home value, reduced HVAC equipment needs, and prevention of moisture-related repairs, closed-cell foam offers compelling long-term financial benefits.
Can closed-cell spray foam be installed in my existing finished Bellevue home?
Yes, though the process differs from new construction. Installers can access wall cavities through small openings that are later repaired, or during planned renovations when walls or ceilings are exposed. Unfinished spaces like crawlspaces, attics, and basements offer easier installation access. Professional installers familiar with Bellevue homes can recommend the least invasive approach for your specific situation.
Making the Right Decision for Your Bellevue Home
Closed-cell spray foam insulation offers Bellevue homeowners superior energy efficiency, moisture control, and building protection. Its performance characteristics align particularly well with the region's climate challenges and energy costs. While requiring higher initial investment than traditional insulation methods, the long-term benefits make it an excellent choice for many Bellevue properties.
When evaluating your insulation options, consider your home's specific needs, your long-term ownership plans, and the particular moisture and temperature challenges of your property's location. The performance advantages of closed-cell spray foam often make it the most cost-effective solution when all factors are considered.
Ready to Improve Your Home's Energy Performance?
Apply these insights to make an informed decision about your Bellevue home's insulation needs. For expert assessment and professional installation, contact Cascadia Spray Foam of Seattle at (425) 386-3500 or info@cascadiasprayfoam.com.
Reviewer:
Olivia Thompson has spent 10 years working in spray foam insulation, helping companies grow their visibility. She reviewed this article and provided valuable suggestions on how to better align the content with the needs and expectations of customers, ensuring it resonates with the target audience.