Built-Up Roof Categories, Materials, and Their Lifespan in Different Climates:
This guide will explore the diverse types of built-up roofing, the materials used, and how various climates affect their performance and longevity.
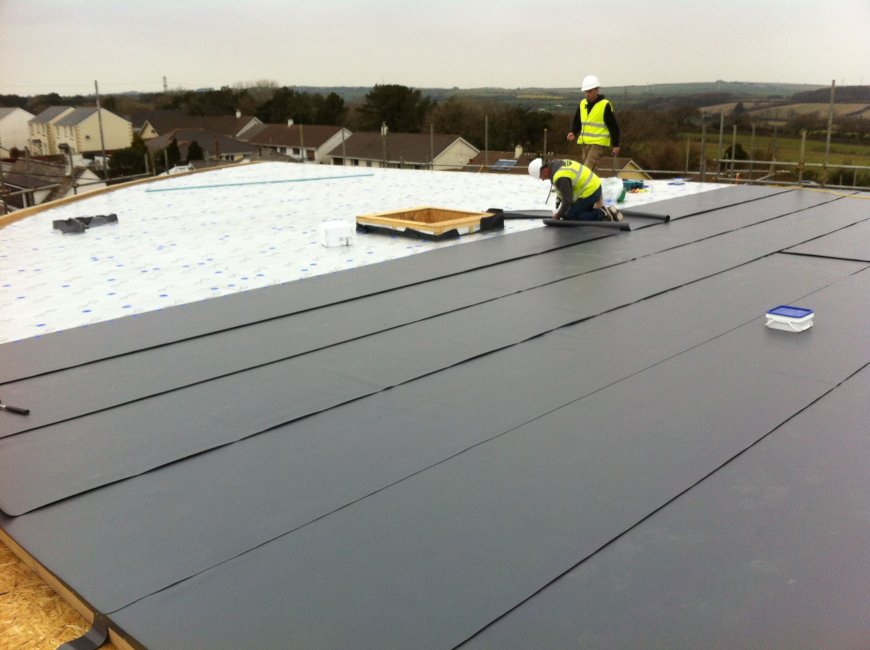
Built-Up Roofs:
Built-up roofing (BUR) systems have been a staple in commercial and flat-roof construction for over a century. Identified for their stability and weather resistance, BUR systems are comprised of several layers of bitumen and supporting materials. These layers are alternated to create a finished membrane that offers superior protection against the elements.
What Is a Built-Up Roof?
Built-Up Roofs consist of three main components:
1. Base Sheet: Installed directly on the roof deck.
2. Reinforcing Ply Sheets: Layers of fiberglass or organic felt embedded in bitumen.
3. Surfacing: Options include gravel, mineral cap sheets, or reflective coatings to protect against UV rays and weather damage.
These layers are bonded together using hot or cold bitumen, creating a watertight barrier.
Types of Built-Up Roof Systems
Hot-Mopped Asphalt BUR
This traditional BUR system uses heated asphalt to bond layers. The hot-mop process creates a strong, seamless finish.
· Advantages: Long-lasting, excellent waterproofing, proven track record.
· Disadvantages: It requires specialized equipment and produces fumes during installation.
Cold-Applied BUR
Cold-applied systems use bituminous adhesives that don't require heating.
· Advantages: Safer installation, fewer emissions, suitable for occupied buildings.
· Disadvantages: Slower curing time, potentially higher material costs.
Ballasted BUR
· Advantages: UV protection, wind resistance, natural fire resistance.
· Disadvantages: Heavy, may require reinforced structural support.
Modified Bitumen Hybrid
Combines traditional BUR with modified bitumen membranes.
· Advantages: Enhanced elasticity and strength, greater adaptability to temperature changes.
· Disadvantages: Higher cost, complex installation.
Common Materials Used in BUR Systems
Bitumen
Bitumen is the main waterproofing factor in built-up roofing (BUR) systems. It may be asphalt, coal tar, or a cold-applied adhesive. Asphalt is the most utilized option due to its affordability and dependable performance.
Reinforcing Fabrics
These materials consist of fiberglass mats or organic felts, which enhance the roof's tensile strength and structural stability. Fiberglass is preferred for its non-rotting properties and resistance to fire and moisture.
Surfacing Options
· Gravel: Protects against UV rays and mechanical damage.
· Mineral-Surfaced Cap Sheets: Provide a finished appearance and additional weatherproofing.
· Reflective Coatings: Reduce heat absorption, improving energy efficiency.
Lifespan of BUR Systems by Climate
The lifespan of a built-up roof can vary significantly depending on the climate in which it is installed. Let’s explore how BUR systems perform in different environments.
Hot and Arid Climates
In regions with high temperatures and minimal rainfall, such as the Southwestern United States:
· Performance: Excellent, especially with reflective surfacing.
· Expected Lifespan: 20-30 years.
· Best Materials: Reflective coatings and fiberglass reinforcements to withstand thermal expansion.
Cold and Snowy Climates
· Performance: Very good if proper drainage and insulation are in place.
· Expected Lifespan: 20-25 years.
· Best Materials: Modified bitumen membranes, mineral cap sheets for better snow shedding.
Humid and Rainy Climates
In coastal or tropical regions with frequent rain and humidity:
· Performance: Good, provided moisture control and ventilation are adequate.
· Expected Lifespan: 15-20 years.
· Best Materials: Fiberglass reinforcements and gravel surfacing to prevent algae growth.
Windy and Hurricane-Prone Areas
For areas like Florida or the Gulf Coast:
· Performance: Dependent on proper anchoring and ballast.
· Expected Lifespan: 15-20 years.
· Best Materials: Ballasted systems with heavy gravel, reinforced seams, strong adhesives.
Maintenance and Longevity Tips
· Conduct Routine Inspections: Ideally, two times a year, and following significant weather conditions.
· Prompt Repairs: Address blisters, cracks, or punctures immediately.
· Debris Removal: Keep the surface clean to prevent clogging and ponding.
· Re-Coating: Apply protective coatings every 5-10 years as needed.
Roof Inspection Checklist by a Pro Roofing Company:
Exterior Roof Inspection
Shingle Condition:
Check for missing, curling, cracked, or blistered shingles.
Flashing & Seals:
Inspect metal flashing around chimneys, vents, and skylights for rust or separation.
Gutters & Downspouts:
Ensure they are securely attached, free of debris, and draining properly.
Roof Slope & Sagging:
Look for any signs of sagging or uneven surfaces, which could indicate structural issues.
Moss, Algae, or Debris:
Remove organic growth and debris that can trap moisture and degrade roofing materials.
Interior Roof Inspection
Attic Ventilation:
Confirm that air is flowing correctly to prevent heat and moisture buildup.
Signs of Water Damage:
Look for stains, mold, or mildew on rafters and insulation.
Insulation Integrity:
Ensure the insulation is dry and fluffy, not compressed, to maintain optimal energy efficiency.
Safety Features
Anchoring Points:
Ensure ladders and safety gear are secure during inspection.
Edge Protection:
Watch for weak or compromised roof edges.
Conclusion:
Built-up roofing systems remain a reliable and durable choice for flat and low-slope roofs. Hiring a professional company like Positive Roofing ensures nothing is overlooked. Routine inspections (ideally twice a year) can help extend your roof’s life and maintain your home’s value.