How CAD Scanning Enhances Quality Control in Industrial Settings
Discover how 3D Scanning is transforming product design and development by improving accuracy, accelerating prototyping, and streamlining workflows across industries. Learn how Nel Pretech Corporation helps businesses innovate faster with cutting-edge 3D scanning solutions.
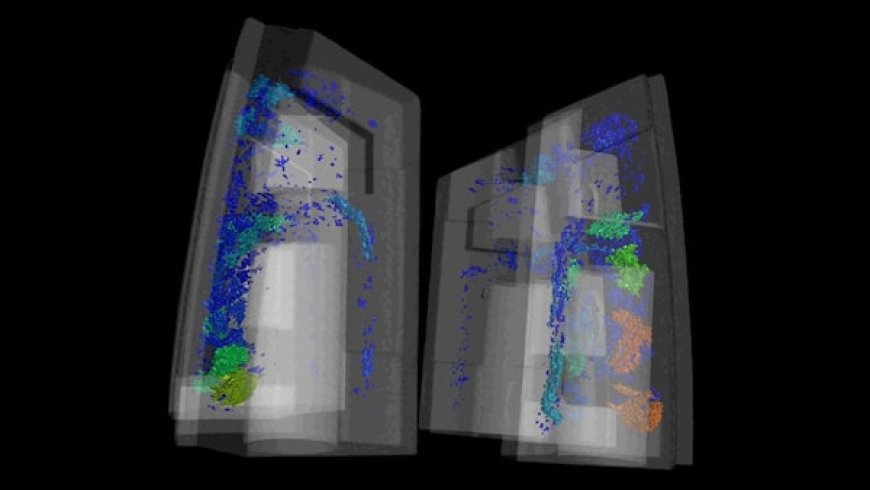
In today's fast-paced and competitive industrial landscape, innovation and precision are critical to staying ahead. From conceptualization to production, companies are constantly looking for ways to streamline workflows and boost product quality. One of the most transformative technologies aiding this mission is 3D Scanning. It has become an essential tool in the product design and development lifecycle, offering a level of accuracy and efficiency that traditional methods often lack.
Whether it’s reverse engineering a legacy part, validating design integrity, or accelerating prototyping, 3D Scanning is helping businesses reduce errors, save time, and bring better products to market faster. This article explores how 3D Scanning enhances each phase of product design and development and why companies across industries are rapidly adopting this powerful technology.
What is 3D Scanning?
3D Scanning is the process of capturing a physical object’s exact shape and dimensions using laser or structured light scanners. The scanned data is used to create high-resolution 3D models known as point clouds or mesh models, which can be further refined in CAD software. These digital representations are incredibly precise, often down to microns, making them ideal for a wide range of applications including design, analysis, simulation, and quality control.
From automotive and aerospace to consumer goods and healthcare, the application of 3D Scanning continues to grow as industries demand faster, more accurate design validation and product development processes.
Improving Conceptual Design with 3D Scanning
During the initial phase of product development, designers often work with rough sketches, clay models, or early prototypes. This is where 3D Scanning offers a distinct advantage. By scanning these physical models, designers can quickly convert them into editable 3D CAD models. This seamless transition from physical to digital reduces manual modeling time and ensures that creative ideas are preserved with utmost precision.
Moreover, 3D Scanning allows designers to make real-time modifications and explore design alternatives more efficiently. Instead of starting from scratch with each iteration, scanned data can be reused, saving both time and resources.
Accelerating Reverse Engineering
Reverse engineering is an integral part of modern product development—especially when dealing with legacy parts or competitor products. Traditionally, reverse engineering involved manual measurements and time-consuming modeling. But with 3D Scanning, engineers can now capture every detail of a complex component within minutes.
This technology enables the recreation of accurate CAD models of outdated parts that have no existing design documentation. These models can then be analyzed, modified, or even improved to meet new performance standards. Whether it’s for redesign, replacement, or integration into new systems, 3D Scanning simplifies the entire reverse engineering process.
Enhancing Prototyping and Iteration
The prototyping stage is crucial for testing and validating product functionality before full-scale production. 3D Scanning enhances this phase by enabling designers to quickly scan and analyze physical prototypes. Any inconsistencies or dimensional deviations can be identified early and corrected before further investment is made.
By integrating 3D Scanning into the prototyping workflow, development teams can iterate designs faster and with greater confidence. Combined with 3D printing or CNC machining, this technology creates a feedback loop that accelerates innovation and shortens the product development cycle.
Ensuring Quality Control and Inspection
One of the most impactful uses of 3D Scanning is in quality assurance and inspection. Traditional methods often rely on coordinate measuring machines (CMMs) or manual tools, which can be time-consuming and limited in scope. 3D Scanning, on the other hand, provides a non-contact, full-surface measurement of components, allowing for comprehensive inspection.
Manufacturers can compare scanned data with CAD models to ensure that parts meet design specifications. Heat maps, deviation analysis, and dimensional reports generated from scanned data help in maintaining product quality and consistency throughout the production line.
Streamlining Collaboration and Communication
In any product development project, communication between cross-functional teams is vital. 3D Scanning simplifies collaboration by providing accurate, visual representations of physical products that can be shared across departments and even continents. Engineers, designers, and manufacturers can all work from the same data set, reducing misunderstandings and rework.
Additionally, 3D Scanning supports digital workflows and integrations with popular CAD and PLM platforms. This digital continuity ensures that every stakeholder has access to updated and precise information throughout the product lifecycle.
Applications Across Industries
The versatility of 3D Scanning makes it a valuable asset across a variety of industries:
-
Automotive: Reverse engineering, crash analysis, design validation.
-
Aerospace: Inspection of complex parts, maintenance of legacy aircraft components.
-
Consumer Electronics: Rapid prototyping, ergonomic design testing.
-
Healthcare: Custom prosthetics, dental implants, orthopedic analysis.
-
Architecture and Construction: As-built documentation, renovation planning.
In each of these sectors, 3D Scanning enables greater accuracy, flexibility, and efficiency—resulting in better products and customer satisfaction.
Future Trends in 3D Scanning
The future of 3D Scanning looks even more promising with the rise of AI, automation, and cloud computing. AI-powered scanning systems are making it easier to detect anomalies and suggest corrective actions. Meanwhile, automated scanning arms and mobile handheld devices are making the technology more accessible and user-friendly.
Cloud-based platforms are also allowing teams to store, share, and analyze scanned data in real-time, regardless of location. As hardware becomes more compact and software becomes more intelligent, 3D Scanning will continue to be a cornerstone of digital transformation in manufacturing and product design.
Conclusion
3D Scanning is no longer a luxury—it’s a necessity for companies that want to stay ahead in design innovation and product excellence. By enabling faster iterations, more accurate designs, and higher quality assurance, this technology is reshaping the way products are imagined, developed, and brought to market.
From ideation to inspection, the advantages of 3D Scanning are undeniable. Businesses looking to improve their design and development workflows should consider integrating this powerful tool into their processes.