Understanding the Process Behind Masonry Estimating Services: A Step-by-Step Guide
Masonry estimating services play a crucial role in the construction industry. From residential buildings to large commercial projects,
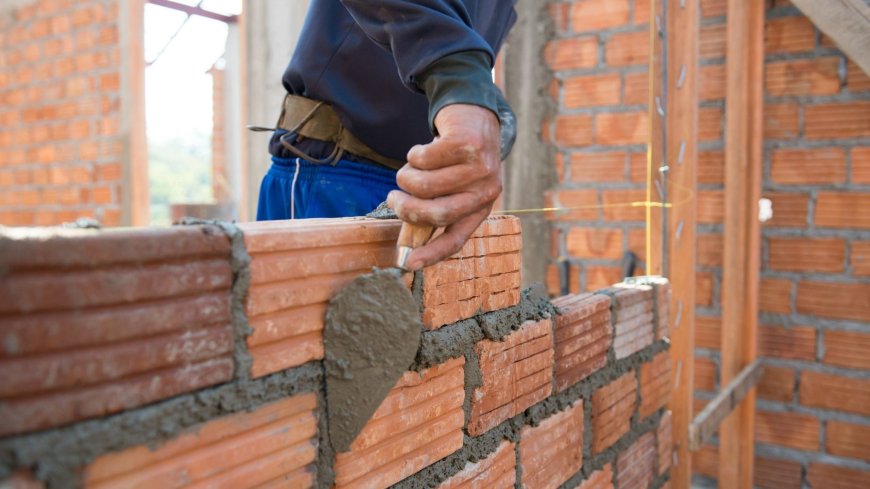
Masonry estimating services play a crucial role in the construction industry. From residential buildings to large commercial projects, masonry work involves intricate calculations and precise planning to ensure the project is completed within budget and on schedule. Accurate masonry estimating not only helps in managing costs but also ensures the proper allocation of resources. In this guide, we’ll walk you through the step-by-step process of masonry estimating services, explaining how professionals approach the task and the factors they consider to produce an accurate estimate for your project.
Step 1: Initial Project Assessment
Before any calculations begin, the first step in masonry estimating is a thorough assessment of the project. The estimator needs to understand the scope of the work, the materials required, and the complexity of the design. This is typically done through a detailed review of the project plans or blueprints.
Key Considerations:
-
Blueprints and Drawings: Estimators review architectural plans, drawings, and specifications to understand the exact requirements of the masonry work. This includes the type of masonry (e.g., brick, stone, concrete block), the size of the project, and any specific details such as structural elements, design features, or finishes.
-
Project Scope: The scope of work is determined by identifying the areas of the project that will involve masonry. Whether it's a retaining wall, foundation, or decorative brickwork, understanding the full scope allows the estimator to plan the resources and time accurately.
-
Site Conditions: Factors such as site access, weather conditions, and the complexity of the terrain are also considered during this stage, as they can impact the cost and timeline.
Why It’s Important:
Accurate project assessment ensures that the estimator has a clear understanding of what the project entails. Without this step, any estimates could be based on incomplete or incorrect information, leading to underestimations or overestimations.
Step 2: Quantity Takeoff
The next step is the quantity takeoff, where the estimator calculates the exact amount of materials needed for the project. This is one of the most critical aspects of the estimating process because it directly impacts both the cost and timeline of the project.
Key Considerations:
-
Material Calculations: The estimator calculates the quantity of bricks, blocks, mortar, and any other materials required for the project. They will carefully count the number of units (bricks, stones, etc.) needed to cover the area specified in the plans, accounting for the dimensions and complexity of the structure.
-
Waste Factor: A certain percentage of material is usually added to account for wastage during the masonry process (e.g., breakage, cuts, etc.). This ensures that enough material is ordered to complete the work without unnecessary delays.
-
Labor Requirements: Along with the material quantities, labor requirements are also estimated based on the scope of work. This includes the number of workers needed and the total number of labor hours required to complete the project.
Why It’s Important:
The accuracy of the quantity takeoff determines the success of the estimate. Underestimating material quantities can lead to shortages during construction, while overestimating can result in excess inventory and wasted resources. Additionally, estimating labor hours helps avoid unnecessary delays and keep costs under control.
Step 3: Cost Estimation
After the quantity takeoff is completed, the next step is to assign costs to the materials, labor, and equipment needed for the project. This involves working closely with suppliers, subcontractors, and vendors to obtain current prices for the materials and labor.
Key Considerations:
-
Material Prices: The estimator will get current prices for all the materials involved in the project. This includes everything from bricks and mortar to specialized materials like stone or decorative finishes. Prices can vary depending on location, supplier, and market conditions.
-
Labor Rates: Labor costs are another significant component of the overall estimate. The estimator will take into account the number of workers, the skill level required, and the regional labor rates to determine the total cost for labor.
-
Equipment and Tools: If any specialized tools or equipment are required for the masonry work (e.g., scaffolding, cranes, mixers), these costs will be included in the estimate as well. The estimator will calculate how much time the equipment will be used and the associated rental or operating costs.
-
Overhead and Profit Margins: Contractors also add overhead costs (such as insurance, office expenses, and project management fees) and desired profit margins. These are factored into the final estimate to ensure the business remains profitable.
Why It’s Important:
The accuracy of the cost estimation directly impacts the financial viability of the project. If the estimate is too low, the project may exceed budget, causing financial strain. Conversely, overestimating costs could result in lost contracts due to uncompetitive pricing.
Step 4: Risk Assessment and Contingency Planning
Masonry projects, like any other construction work, come with risks. Estimators need to consider potential issues that could arise during construction, such as weather delays, material shortages, or unexpected site conditions. Risk assessment helps ensure that the project remains within budget and on schedule, even if unforeseen circumstances occur.
Key Considerations:
-
Unforeseen Conditions: Estimators assess the likelihood of unforeseen issues, such as changes in the site conditions, which could increase costs or extend timelines.
-
Weather Considerations: Inclement weather, such as heavy rain or snow, can cause delays, especially if outdoor masonry work is involved. Estimators factor in possible weather disruptions when developing timelines and budgets.
-
Contingency Budgets: A contingency allowance is often included in the estimate to cover potential risks. This is typically a percentage of the total project cost and can be used to address unforeseen complications without derailing the project’s finances.
Why It’s Important:
Risk assessment and contingency planning help safeguard the project’s success by preparing for potential challenges. A well-prepared estimate that accounts for risks can prevent unexpected expenses and delays, which ultimately saves time and money.
Step 5: Finalizing the Estimate
Once all of the calculations are complete and costs have been assigned to materials, labor, and equipment, the final estimate is prepared. This estimate is a detailed, comprehensive breakdown of all the expenses required to complete the masonry work, and it is typically presented in a report or proposal format for the client or project manager.
Key Considerations:
-
Comprehensive Breakdown: The final estimate includes detailed descriptions of all the costs involved, such as materials, labor, equipment, overhead, and profit margins. This level of detail ensures that both the contractor and client have a clear understanding of the project’s financial requirements.
-
Client Review and Approval: Once the estimate is finalized, it is presented to the client for review. The client can ask questions or request clarifications before giving final approval.
-
Adjustments: Based on client feedback or additional information, the estimator may need to make adjustments to the estimate before it is finalized and submitted.
Why It’s Important:
A finalized estimate provides the project team with a clear financial roadmap for the project. This ensures that the project remains within budget and prevents misunderstandings between the contractor and client regarding costs.
Step 6: Ongoing Monitoring and Adjustments
Even after the estimate is finalized, the process doesn’t end there. During the course of the project, masonry estimators may continue to monitor costs and progress to ensure that the project stays on track.
Key Considerations:
-
Tracking Progress: The estimator or project manager tracks the progress of the work to ensure that it aligns with the initial estimate. If there are any significant deviations, they may need to adjust the budget or timeline.
-
Updating Estimates: If unexpected changes occur (e.g., design changes, additional work), the estimator updates the original estimate to reflect the new scope or requirements.
Why It’s Important:
Ongoing monitoring and adjustments help to keep the project on track. By addressing any deviations from the estimate early on, the project can remain within budget and be completed on time.
Conclusion
Masonry estimating services are an essential part of any construction project, providing a detailed, accurate breakdown of costs, materials, and labor. The process involves multiple steps, from project assessment and quantity takeoff to cost estimation and risk management. Each step plays a critical role in ensuring the success of the project, and a well-executed estimate can save both time and money in the long run. By understanding the process behind masonry estimating, construction businesses can make informed decisions, minimize risks, and complete projects more efficiently.
Related Posts
How Can Selenium Be Used to Extract Data from a Webpage?
Jun 10, 2025 0