Key Benefits of Attic Insulation in Joplin, MO for Energy Savings and Comfort
Attic insulation reduces energy costs by 15-50% in Joplin homes while maintaining consistent indoor temperatures year-round.
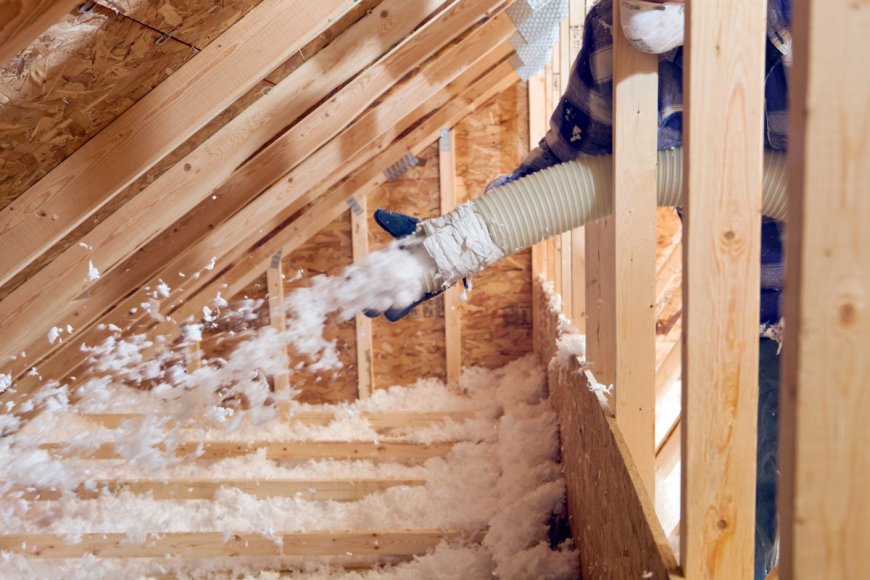
Attic insulation reduces energy costs by 15-50% in Joplin homes while maintaining consistent indoor temperatures year-round. Proper insulation prevents heated and cooled air from escaping through the roof, creating a thermal barrier that protects against Missouri's extreme temperature variations ranging from sub-zero winters to 100°F+ summers.
The primary benefits of hiring a professional attic insulation contractor include lower utility bills, improved comfort levels, reduced HVAC system strain, and enhanced indoor air quality. Joplin's climate demands robust thermal protection, as inadequate attic insulation forces heating and cooling systems to work continuously, driving up energy consumption and equipment wear while failing to maintain comfortable living conditions.
Energy Cost Reduction Analysis
Attic insulation directly impacts energy consumption by preventing thermal transfer between conditioned living spaces and outdoor temperatures. Heat naturally rises and escapes through inadequately insulated attics during winter months, while summer heat penetrates downward into living areas, forcing HVAC systems to compensate continuously.
Market data from the Department of Energy indicates that Missouri homeowners save an average of $400-800 annually on utility bills after upgrading attic insulation to current R-value standards. These savings compound over time, with properly insulated attics reducing total home energy consumption by 20-40% depending on existing conditions.
Immediate Comfort Improvements
Temperature consistency throughout the home improves dramatically with adequate attic insulation. Hot and cold spots disappear as the thermal envelope prevents outdoor temperature fluctuations from affecting interior comfort levels. Second-floor rooms maintain comfortable temperatures without requiring excessive heating or cooling adjustments.
Draft elimination occurs when air sealing accompanies insulation installation, preventing conditioned air from escaping through attic penetrations and gaps around fixtures, outlets, and structural components.
Bonus Tip: Combine attic insulation with air sealing around recessed lights, electrical boxes, and plumbing penetrations for maximum energy efficiency gains.
Insulation Material Comparison
Material Type |
R-Value per Inch |
Longevity |
Moisture Resistance |
Installation Method |
Cost Range |
Spray Foam (Closed-Cell) |
R-6.0 - R-7.0 |
30+ years |
Excellent |
Professional |
$$$ |
Spray Foam (Open-Cell) |
R-3.5 - R-4.0 |
25+ years |
Good |
Professional |
$$ |
Blown-in Cellulose |
R-3.2 - R-3.8 |
20-25 years |
Fair |
Professional |
$ |
Fiberglass Batts |
R-3.1 - R-3.4 |
15-20 years |
Poor |
DIY/Professional |
$ |
Blown-in Fiberglass |
R-2.2 - R-4.3 |
15-20 years |
Fair |
Professional |
$ |
Climate-Specific Performance for Joplin Region
Joplin's continental climate creates challenging conditions for attic insulation systems. Summer temperatures regularly exceed 90°F with high humidity levels, while winter lows drop below 20°F with significant temperature swings. These conditions test insulation materials' ability to maintain thermal performance and resist moisture infiltration.
The region's severe weather patterns, including tornado activity and hailstorms, place additional stress on roofing systems that can compromise insulation effectiveness. Properly installed insulation maintains performance even when minor roof damage allows limited moisture intrusion.
Humidity Management Benefits
Attic insulation helps control indoor humidity levels by preventing moisture-laden outdoor air from infiltrating living spaces through thermal bypasses. This moisture control reduces the risk of mold growth, wood rot, and indoor air quality problems that plague homes with inadequate thermal barriers.
Proper insulation also prevents ice dam formation during winter months by maintaining consistent roof surface temperatures, protecting gutters and roof edges from freeze-thaw damage cycles.
HVAC System Efficiency Enhancement
Reduced system runtime occurs when attic insulation minimizes thermal loads on heating and cooling equipment. HVAC systems reach target temperatures faster and maintain comfort levels with shorter operating cycles, extending equipment lifespan and reducing maintenance requirements.
Energy recovery improves as conditioned air remains within the thermal envelope instead of escaping through attic spaces. This retained energy reduces the total heating and cooling load by 25-45% in typical Missouri homes.
Bonus Tip: Upgrade to programmable thermostats after insulation installation to maximize energy savings through optimized temperature scheduling.
Technical Performance Standards
Performance Metric |
Current Code Requirement |
Recommended Level |
High-Performance Target |
Minimum R-Value (Zone 4) |
R-38 |
R-49 |
R-60 |
Air Leakage Rate |
< 7.0 ACH50 |
< 5.0 ACH50 |
< 3.0 ACH50 |
Vapor Permeability |
Climate appropriate |
< 1.0 perm (closed-cell) |
Material dependent |
Fire Rating |
Class A or 1 |
Class A or 1 |
Class A or 1 |
Settled Thickness |
90% retention |
95% retention |
No settling (spray foam) |
Operating Temperature |
-40°F to 180°F |
-40°F to 200°F |
Material dependent |
Long-Term Durability Factors
Material degradation varies significantly among insulation types, affecting long-term performance and replacement costs. Spray foam maintains consistent R-values throughout its lifespan, while blown-in materials may settle or compact over time, reducing thermal effectiveness.
Pest resistance becomes important in attic environments where rodents and insects may nest or travel. Certain insulation materials provide better resistance to pest infiltration and damage, maintaining thermal performance and indoor air quality.
Moisture tolerance affects insulation longevity, particularly in attic spaces where roof leaks or ice dams may introduce water. Materials with poor moisture resistance require replacement after water exposure, while others maintain performance when properly dried.
Installation Quality Impact
Professional installation ensures proper coverage density, air sealing, and ventilation maintenance that DIY approaches often miss. Gaps, compression, and inadequate air sealing can reduce insulation effectiveness by 30-50%, negating potential energy savings.
Code compliance verification protects homeowners from future issues when selling or refinancing properties. Professional installers understand local building codes and inspection requirements that affect project approval and insurance coverage.
Things to Consider Before Making a Decision
Evaluate your current insulation levels and condition before selecting upgrade strategies. Homes built before 1980 typically have minimal insulation, while newer construction may only need supplemental coverage to meet current efficiency standards.
Consider attic accessibility and storage requirements when choosing insulation types. Blown-in materials work well in tight spaces but may interfere with storage use, while batt insulation allows easier access for maintenance activities.
Budget for complementary improvements like air sealing, ventilation upgrades, and electrical modifications that maximize insulation effectiveness. These additional costs provide significant returns through enhanced performance and system longevity.
Assess seasonal timing for installation projects. Spring and fall offer ideal weather conditions for attic work, while summer and winter installations may face comfort and safety challenges that affect project scheduling and costs.
Existing Infrastructure Evaluation
Examine electrical systems, HVAC ductwork, and plumbing components in attic spaces before hiring an insulation installation service in Joplin, MO. Older systems may require updates or modifications to accommodate new insulation levels and maintain safe operating conditions.
Review homeowner's insurance policies regarding insulation upgrades and potential premium reductions. Many insurers offer discounts for energy efficiency improvements that reduce claim risks and property values.
Common Questions
Ventilation requirements change with insulation upgrades: Maintaining proper attic ventilation prevents moisture accumulation and temperature extremes that can damage roofing materials. Soffit and ridge vents must remain unobstructed regardless of insulation type.
Energy rebate programs availability: Local utility companies and government agencies offer rebates for insulation upgrades that meet specific R-value requirements. These incentives can offset 10-30% of total project costs.
Timeline expectations for energy savings: Most homeowners notice immediate comfort improvements, while utility bill reductions become apparent within the first complete billing cycle after installation completion.
Integration with solar energy systems: Attic insulation enhances solar panel efficiency by reducing cooling loads and improving overall home energy performance, maximizing renewable energy investment returns.
Bonus Tip: Schedule professional energy audits before and after insulation installation to document performance improvements and qualify for maximum available rebates.
Frequently Asked Questions
How much insulation does my Joplin attic need? Missouri building codes require minimum R-38 insulation, but R-49 to R-60 provides optimal energy savings for the region's climate conditions and typical energy costs.
Can new insulation be added over existing materials? Yes, most insulation types can be layered over existing materials, though removing old, damaged, or contaminated insulation often provides better long-term results.
What's the payback period for attic insulation investment? Most homeowners recover insulation costs within 2-7 years through energy savings, depending on existing conditions, material choices, and local utility rates.
Does attic insulation help with noise reduction? Insulation materials provide moderate noise reduction from outdoor sounds, aircraft, and weather, though acoustic performance varies significantly among material types.
How long does professional installation typically take? Most residential attic insulation projects complete within 4-8 hours, depending on home size, access conditions, and required preparation work.
Ready to Achieve Maximum Energy Efficiency
Attic insulation delivers measurable energy savings, enhanced comfort, and improved home value through reduced utility costs and HVAC system efficiency. The investment provides immediate comfort improvements while generating long-term financial returns that increase with rising energy costs.
Ozark Eco Foam Insulation brings specialized expertise in Missouri climate conditions and building requirements, ensuring optimal insulation solutions tailored to each home's specific needs. Professional assessment identifies the most cost-effective upgrade strategies that maximize energy performance and comfort improvements.
Contact Ozark Eco Foam Insulation today to schedule your comprehensive attic insulation evaluation: Ozark Eco Foam Insulation, (620) 383-9092, ozarkecofoam@gmail.com.
Author and Reviewer
Author: Jeremy Fields brings over a decade of experience in construction and business to Ozark Eco Foam. With a background in both residential and commercial projects, he focuses on completing each insulation job with accuracy and attention to detail. Ozark Eco Foam reflects his commitment to quality work and practical solutions built on years of hands-on industry knowledge.
Reviewer: Amelia Young contributed insights from 10 years in spray foam insulation. Her review helped sharpen the article's focus on customer engagement and clear service messaging.