The Complexities of Display Box Manufacturing Detail Knowledge
Read how complicated assembly operations modify production effectiveness in today's retail display box industry.
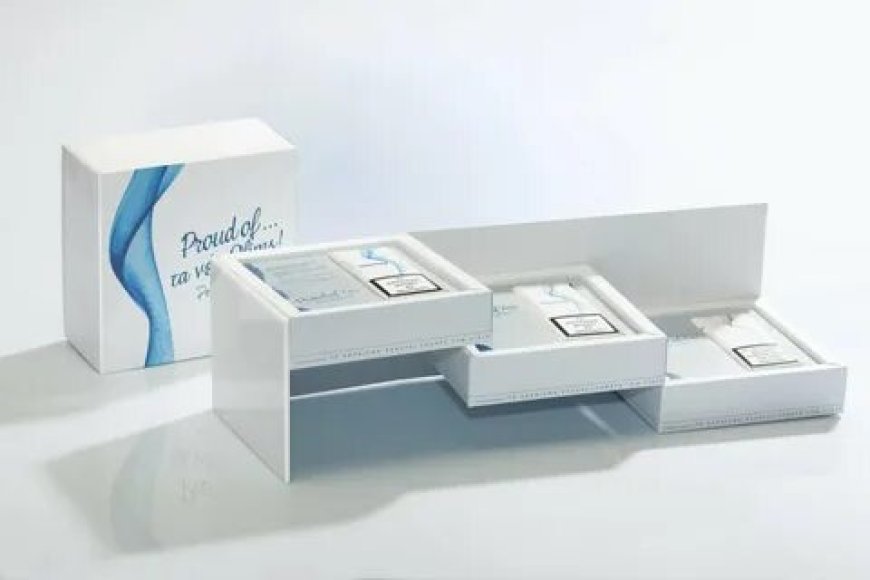
Fast-moving activities within retail packaging demand daily adjustments between operational speed and creative packaging solutions. Assembly complexity represents a major factor in manufacturing operations since it describes the level of difficulty involved in packaging assembly procedures. The process to assemble attractive packages affects the time spent on manufacturing operations and worker expenditure as well as product operational capabilities.
The modern manufacturing industry encounters numerous obstacles during the production of boxes designed to attract attention and support products. The overall package complexity results from each successive design choice and material selection and structural design element. The display box industry requires innovative solutions to be cost-effective.
The growing market need for innovative packaging solutions creates an expanded importance of assembly complexity evaluation. Organizations that produce box products must equally focus on visual design elements with manufacturing requirements for all their packaging solutions. Strategic combinations between elements lead to retail achievements according to the information presented in this article.
The Assembly Dilemma
The main manufacturing challenge in display boxes wholesale production arises from design freedom competition with assembly construction requirements. The combination of detailed cut design and foldable compartments with die-cut windows results in attractive appearance features that create longer assembly times. The number of additional features directly affects construction time, which drives up labor expenses and production costs.
The foam plastic assembly process faces two major constraints when developing cardboard display boxes with dual functions of attractive product presentation and mechanical stability under weight. When a box demands folding along with locking and gluing operations at multiple process stages it automatically lengthens the production schedule. Manufacturers usually need to buy skilled operators or purchase automated production tools when they handle complex designs.
The packaging industry expects retailers to chose boxes with simple setup procedures while the boxes also need sturdiness when placed on store shelves. Manufacturers should create boxes which fulfill industry requirements and production affordability standards. A manufacturer must manage multiple factors to determine how well their brand performs in the marketplace.
The Role of Materials in Assembly Complexity
The selection of materials determines the extent of assembly difficulties that a display box presents. Easier handling is a main advantage of lightweight materials but the design elements that brands need typically remain unsupported with them. Using heavy materials helps packaging retain durability yet their precise handling during creation makes assembly procedures more complicated.
The packaging innovations in display boxes in canada frequently use sustainable materials derived from recycled goods to suit environmental shifts. The irregular tendencies of these materials during folding and gluing periods necessitate unique modifications in production. The number of required alterations drives increased complexity in the assembly procedure.
The outcome of printing, scoring, and bending procedures varies with different materials because each substance responds differently to such manipulations. Production companies must identify how each material responds to assembly pressure to guarantee that their packages stay effective and appealing.
Customization and Its Complications
Custom packaging solutions demonstrate great economic value because they enable brands to stay visible in competitive retail markets. Designs and shapes that are customized require manufacturers to face increased complexity throughout operations. Implementing new features such as fold-out compartments or transparent panels advances assembly steps due to their addition to the system.
Custom display boxes that serve specific products usually contain special features that make production extremely challenging. All customized designs need to undergo prototype testing and then require detailed plans that ensure efficient assembly with maintained quality standards.
The escalating market need for distinctive packaging forces manufacturers to improve their manufacturing processes constantly. Close collaboration takes place between designers and clients to transform ideas into practical realizations at a reasonable expense. Manufacturing a product from start to finish involves a complex evolution between original design and store availability.
How Retail Requirements Influence Assembly
Retail businesses establish particular requirements that determine how manufacturers design and assemble packaging formats. The essential elements retailers demand from their boxes encompass aesthetic appeal, practical usage, a nd restocking simplicity with uniform product quality. The addition of features such as locking tabs, insert holders, and product stabilizers complicates the manufacturing process of the boxes to meet the specialized requirements of retailers.
Display boxes designed for retail operations must be flexible to synchronize with various retail fixtures found in store layouts. The product's performance in every retail environment requires manufacturers to include these diverse factors in both design specifications and assembly procedures.
The buying patterns of retailers include bulk quantity orders with tight delivery requirements. The processing needs to operate at optimal capacity regardless of the complex nature of package designs. The problem puts both manufacturing speed and product design thinking under intense evaluation.
Innovation vs. Production Efficiency
Business success in the packaging industry depends on innovation but technical advancement may result in diminished manufacturing performance levels. The implementation of new features or formats in production lines results in delays unless production lines have been optimized for enhanced complexity. Your choice in this situation involves picking between quick delivery or innovative solutions.
The creation of custom cardboard display boxes introduces die-cuts and pop-up elements and multiple compartments within them. Many visually impressive designs that enhance product visibility demand higher amounts of manual labor and specialized assembly equipment. The assembly process becomes delayed by additional complexities that create more opportunities for human mistakes or inconsistent results.
The progress of technology allows automation systems to reduce various manufacturing problems. Manufacturers need to conduct thorough tests to verify if each new assembly technique will succeed in production. A fantastic design remains beneficial only when manufacturers can execute mass production without delays or production mistakes.
Wholesale Production Complexities
The process of making larger quantities presents fresh difficulties. Large-scale production exposes and amplifies every production inefficiency that remains in the process. The manufacturing methods that proved successful for small production quantities fail to scale up properly for extensive production runs. Standardization needs to be a priority, yet it proves difficult to achieve while working with specific and feature-abundant designs.
The production requirement becomes particularly significant for products such as display boxes because, typically, numerous thousands of units need rapid manufacturing. The assembly process needs both manufacturing automation assessments and skilled labor evaluation for cost analysis purposes.
The businesses operating in wholesale triangle boxes sales or window display box catering need to maintain solution-wide consistency in box quality standards. The product quality consistency faces jeopardy from complex assembly procedures that need proper management. The business model of retail clients demands strict adherence to precise operation and timely delivery during high-volume production.
Final Thoughts
The realm of display packaging demands multiple levels of complication, which function as both vital requirements and substantial obstacles. The combination of innovation through complexity and visual appeal requires well-organized planning together with efficient methods of assembly and smart resource utilization. The ability of manufacturers to handle complexity successfully leads to the creation of better products that achieve successful retail performance.
To succeed in display packing box production, manufacturers should maintain an equilibrium between inventive designs and functional specifications regardless of whether they focus on wholesale or retail applications. Packages need to stay simple enough to support operational efficiency and customer contentment.
Brands constantly seek innovative packaging approaches which force manufacturers to keep developing their solutions. By committing resources to design advancements, improved materials and fast production techniques businesses can reduce the negative effects from complexity. The path to success relies on achieving functional creativity at its highest level.