This Brooklyn apartment complex was built like a Lego set
When construction started on a new affordable apartment building in Brooklyn, most of the work on the site happened very quickly. Instead of typical construction, cranes lifted giant modular units into the air—each made up of two separate apartments, plus the corridor between them—and set them into place. Trucks delivered nearly four dozen 60-foot-long “mods” from the factory where they were built in Pennsylvania, staging them next to a nearby cemetery in the Brooklyn neighborhood of East Flatbush. Then, each day for two weeks, construction crews stacked together as many as six of the units. (The massive size of the units made them more challenging to transport than a single modular apartment at a time, but the configuration helped shrink the time for installation on site.) [Photo: courtesy RiseBoro] The apartments were essentially 100% complete inside. (Appliances were strapped to the corridors and just had to be slid into place.) The crew only had to weld the units together and connect wiring and plumbing from each apartment to the hallway. After all of the units were attached, the crew added continuous insulation to the outside and finished other elements like the roof. [Image: courtesy RiseBoro] A project of this size, with 57 apartments and four stories, could have taken 30 months to build, says Yolanda do Campo, director of construction at RiseBoro, the nonprofit developer behind the project. Instead, it took only 22 months. A shorter timeline means significant savings. “Less construction time means fewer months of interest payments,” do Campo says. Interest payments for the project average around $100,000 a month. It also means, of course, that residents can start moving in faster. In this case, the apartments are limited to seniors in New York City’s affordable housing lottery, with a percentage of the units reserved for seniors who were previously homeless. The process has still taken time, in part because of the bureaucracy involved with the housing lottery. The building was completed last fall; the first residents started moving in in January and only a handful live there so far. But faster construction helped. [Image: courtesy RiseBoro] As builders gain more experience in modular construction, it could happen even more quickly. “I really do think that we do this a couple more times and we’re seeing a building come in 15, 16 months, which is somewhat unheard of for something like this,” says Grayson Jordan, principal at PCA, the architecture firm behind the building’s design. While modular apartment buildings are starting to become more common in cities, the project went a step further with a “passive house” design, meaning that it has ultra-low energy demand. The building is well-insulated and airtight. The hot water system runs on a heat pump. The apartments are all-electric and designed to run on solar power, so the building can get as close to net zero energy use as possible. “RiseBoro pays for some of the utilities of the tenants,” says do Campo. “So being passive house and saving energy is critical to the business model—besides contributing to sustainability, we lower the monthly bills.” RiseBoro has pioneered energy-efficient design in other projects, including adding sleek new facades to aging apartment buildings to help them shrink energy use by 80%. Outside, the south side of the building has stepped terraces instead of a flat wall, creating a series of outdoor community spaces for residents and more space for solar panels. There was a learning curve to using modular construction; since the local construction crew didn’t have expertise working with modular units, Riseboro had to help coordinate between the factory and the crew on the ground. But it will get easier in the future, Jordan says. “I see a way forward where this becomes just normal construction,” he says. “It does not seem like rocket science. It just seems like, OK, well, you did this the first time. Let’s work out the kinks.” There are some other potential cost advantages to doing most of the work in a factory offsite. Labor in the Pennsylvania factory is less expensive. And crews can build the modular units year-round without delays because of bad weather. Jordan hopes that it also will become standard for larger affordable apartment buildings. “I think it really makes a lot of sense,” he says. “It’s just a matter of really getting the people who make the decisions comfortable with the idea of building a little bit differently than they’re used to . . . I think we all know that there’s a great need for affordable housing, and this is one of several tools that I think could be powerful in meeting that challenge.”
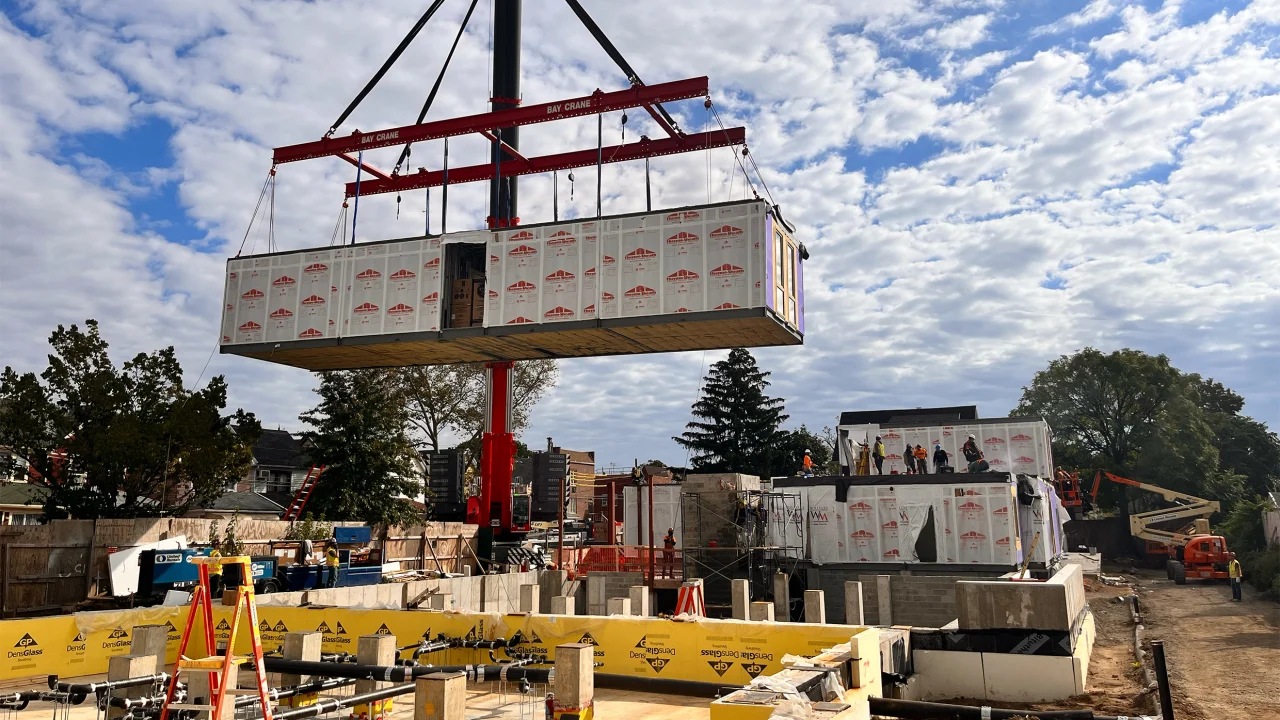
When construction started on a new affordable apartment building in Brooklyn, most of the work on the site happened very quickly. Instead of typical construction, cranes lifted giant modular units into the air—each made up of two separate apartments, plus the corridor between them—and set them into place.
Trucks delivered nearly four dozen 60-foot-long “mods” from the factory where they were built in Pennsylvania, staging them next to a nearby cemetery in the Brooklyn neighborhood of East Flatbush. Then, each day for two weeks, construction crews stacked together as many as six of the units. (The massive size of the units made them more challenging to transport than a single modular apartment at a time, but the configuration helped shrink the time for installation on site.)
The apartments were essentially 100% complete inside. (Appliances were strapped to the corridors and just had to be slid into place.) The crew only had to weld the units together and connect wiring and plumbing from each apartment to the hallway. After all of the units were attached, the crew added continuous insulation to the outside and finished other elements like the roof.
A project of this size, with 57 apartments and four stories, could have taken 30 months to build, says Yolanda do Campo, director of construction at RiseBoro, the nonprofit developer behind the project. Instead, it took only 22 months. A shorter timeline means significant savings. “Less construction time means fewer months of interest payments,” do Campo says. Interest payments for the project average around $100,000 a month.
It also means, of course, that residents can start moving in faster. In this case, the apartments are limited to seniors in New York City’s affordable housing lottery, with a percentage of the units reserved for seniors who were previously homeless. The process has still taken time, in part because of the bureaucracy involved with the housing lottery. The building was completed last fall; the first residents started moving in in January and only a handful live there so far. But faster construction helped.
As builders gain more experience in modular construction, it could happen even more quickly. “I really do think that we do this a couple more times and we’re seeing a building come in 15, 16 months, which is somewhat unheard of for something like this,” says Grayson Jordan, principal at PCA, the architecture firm behind the building’s design.
While modular apartment buildings are starting to become more common in cities, the project went a step further with a “passive house” design, meaning that it has ultra-low energy demand. The building is well-insulated and airtight. The hot water system runs on a heat pump. The apartments are all-electric and designed to run on solar power, so the building can get as close to net zero energy use as possible.
“RiseBoro pays for some of the utilities of the tenants,” says do Campo. “So being passive house and saving energy is critical to the business model—besides contributing to sustainability, we lower the monthly bills.” RiseBoro has pioneered energy-efficient design in other projects, including adding sleek new facades to aging apartment buildings to help them shrink energy use by 80%.
Outside, the south side of the building has stepped terraces instead of a flat wall, creating a series of outdoor community spaces for residents and more space for solar panels.
There was a learning curve to using modular construction; since the local construction crew didn’t have expertise working with modular units, Riseboro had to help coordinate between the factory and the crew on the ground. But it will get easier in the future, Jordan says. “I see a way forward where this becomes just normal construction,” he says. “It does not seem like rocket science. It just seems like, OK, well, you did this the first time. Let’s work out the kinks.”
There are some other potential cost advantages to doing most of the work in a factory offsite. Labor in the Pennsylvania factory is less expensive. And crews can build the modular units year-round without delays because of bad weather.
Jordan hopes that it also will become standard for larger affordable apartment buildings. “I think it really makes a lot of sense,” he says. “It’s just a matter of really getting the people who make the decisions comfortable with the idea of building a little bit differently than they’re used to . . . I think we all know that there’s a great need for affordable housing, and this is one of several tools that I think could be powerful in meeting that challenge.”