All 14 parts of this shoulder bag are made from the exact same material—even the zipper
In a new bag from Freitag, every part—from the fabric to the zipper, straps, buckles, and the thread that holds everything together—is made from a single material. The product is the latest example of a “monomaterial” design approach that some brands are beginning to use for a simple reason: It means that the products can actually be recycled when they eventually wear out. [Image: Freitag] Right now, a typical backpack or bag has components made from multiple different materials. Dismantling everything at the end of its life is too time-consuming and expensive to be feasible. But using one material makes it essentially as simple as recycling a plastic water bottle. “You can basically put that entire product into a shredder instead of taking things apart first,” says Elisabeth Isenegger, who leads international communications at the Switzerland-based, 32-year-old company. Then the material can be melted down and made into pellets to make something new. [Image: Freitag] The company chose a material called polyamide 6, which is commonly used in everything from textiles to toothbrush handles. Because it’s ubiquitous, there’s a market for recycling it. But it was a challenge to find sources for every component that they needed. Freitag also had to find a way to avoid a water-repellent coating that would normally be used on the fabric, but would have made the fabric unrecyclable. To do this, the company worked with one of its suppliers to develop a version of the fabric with three layers, laminated together, that was water repellent on its own. A backpack using the approach came out last year, followed by the smaller new bag, the Musette, that just launched. [Image: Freitag] If something breaks on the bag, consumers can bring it to a Freitag store and then the bag will go to one of the brand’s 10 global repair centers. (The team set up a new repair kit for the backpack and bag, since repairs can also only be made with the same material.) When the bag eventually wears out, consumers can bring it back, and Freitag will work with partners to recycle it; it’s not handled in typical municipal recycling centers. Before launching the first backpack, the company worked with the Switzerland-based Institute for Materials Technology and Plastics Processing to validate the process. Ultimately, Freitag aims to become fully circular in everything that it makes. The brand’s best-known product, messenger bags made from old truck tarps, are already a form of recycling. But the company is now also working with trucking companies to test a new type of tarp material that can also be fully recycled after it’s made into a bag.
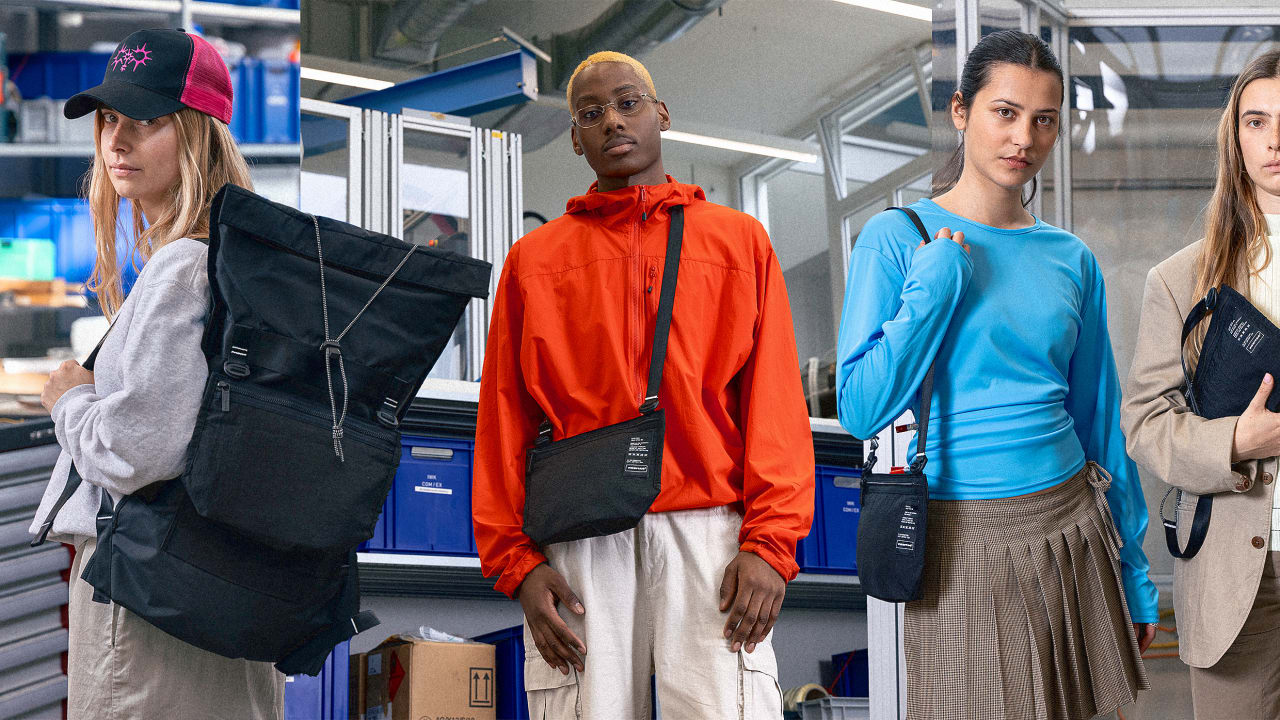
In a new bag from Freitag, every part—from the fabric to the zipper, straps, buckles, and the thread that holds everything together—is made from a single material. The product is the latest example of a “monomaterial” design approach that some brands are beginning to use for a simple reason: It means that the products can actually be recycled when they eventually wear out.
Right now, a typical backpack or bag has components made from multiple different materials. Dismantling everything at the end of its life is too time-consuming and expensive to be feasible. But using one material makes it essentially as simple as recycling a plastic water bottle. “You can basically put that entire product into a shredder instead of taking things apart first,” says Elisabeth Isenegger, who leads international communications at the Switzerland-based, 32-year-old company. Then the material can be melted down and made into pellets to make something new.
The company chose a material called polyamide 6, which is commonly used in everything from textiles to toothbrush handles. Because it’s ubiquitous, there’s a market for recycling it. But it was a challenge to find sources for every component that they needed. Freitag also had to find a way to avoid a water-repellent coating that would normally be used on the fabric, but would have made the fabric unrecyclable. To do this, the company worked with one of its suppliers to develop a version of the fabric with three layers, laminated together, that was water repellent on its own. A backpack using the approach came out last year, followed by the smaller new bag, the Musette, that just launched.
If something breaks on the bag, consumers can bring it to a Freitag store and then the bag will go to one of the brand’s 10 global repair centers. (The team set up a new repair kit for the backpack and bag, since repairs can also only be made with the same material.) When the bag eventually wears out, consumers can bring it back, and Freitag will work with partners to recycle it; it’s not handled in typical municipal recycling centers. Before launching the first backpack, the company worked with the Switzerland-based Institute for Materials Technology and Plastics Processing to validate the process.
Ultimately, Freitag aims to become fully circular in everything that it makes. The brand’s best-known product, messenger bags made from old truck tarps, are already a form of recycling. But the company is now also working with trucking companies to test a new type of tarp material that can also be fully recycled after it’s made into a bag.