Inside the top-secret area of Disney World that theme park visitors and cast members never see
Roughly half a mile behind the Seven Dwarfs Mine Train and Ariel’s Grotto in Walt Disney World sits a nondescript cement warehouse with the words “the can-do people” written on the outside. Should tourists somehow get lost in that corner, located just outside the Magic Kingdom, it’s a place they would never pay attention to. What they might never imagine, however, is that generic building is the lynchpin of the Disney experience. Welcome to Central Shops, a rarely spoken part of Disney that’s off-limits to visitors and most of the company’s cast members (Disney’s term for its employees). It’s ground zero for Disney World’s ride safety and an essential part of park operations around the world. With 417 employees spanning 15 trades, from electricians to carpenters to painters, Central Shops is where every ride in the four Orlando theme parks is regularly inspected to ensure they’re safe to ride. At the same time, it’s also the corner of Disney where character heads for in-park meet-and-greets and parades in all global parks are manufactured. (Put another way, every Goofy, Mickey, Minnie, and Donald you see at the parks had their noggins made here.) [Photo: Disney] Ripping apart Disney World rides Ride inspection is, arguably, the most important job of Central Shops. Every ride vehicle in the four Orlando theme parks ends up here on a recurring basis for inspection—and it’s far from a quick one. Ride vehicles are torn apart, down to their components. Every panel, bolt, etc. is inspected individually, a process that generally takes between 12 and 18 weeks from start to finish, says Fred Cox, director of manufacturing. For dark rides, like a Haunted Mansion Doom Buggy, a log flume from Tiana’s Bayou Adventure, or a horse on Prince Charming’s Carousel, that’s done on a calendar basis, scheduled breaks when select cars are taken out of commission and inspected. For thrill rides, like Space Mountain, it’s meter-based, meaning vehicles are taken off the line after they’ve been ridden a predetermined number of times. On a recent press trip through Central Shops, we saw a number of rides in various states of inspection. A collection of parts on one side was barely identifiable as a ride car from Guardians of the Galaxy: Cosmic Rewind. A few steps away, a honey pot from The Many Adventure of Winnie the Pooh gleamed, following a touch-up to its fiberglass. Sitting off to the side was a disassembled teacup from the Mad Tea Party. And scattered throughout the shop were parts of Astro Orbiter, a ride that has been completely (and temporarily) removed from the Magic Kingdom. Every 10 years, explained Rich Votava, manager of manufacturing, the bearing at the bottom of the ride (which sits atop the People Mover in Tomorrowland) needs to be replaced. Imagineers remove it completely, giving Central Shops a chance to inspect all the ride elements, from the boom arms on the decorative planets on the ride to the ride cars. (The Disney World ride is expected to be back in the park this summer, likely in May or June.) After ride cars are dismantled, each part is carefully inspected, some under X-ray to look for microscopic cracks in the metal. Once each part has been examined and refurbished (if needed), the components of vehicles are put back together, while the shells are repainted or refreshed. Once they are reassembled, cars are then returned to the park, where they run without riders for another two weeks to ensure everything is working properly. After that, visitors begin to pile in once again. (The maintenance schedule of most ride vehicles is staggered so that rides aren’t forced to close completely, like Astro Orbiter has.) “We break it down to the blueprints,” says Votava. Safety inspections go beyond ride vehicles, of course. Workers from Central Shops are in the parks nightly once visitors leave to make any necessary repairs and safety inspections for rides. Sometimes, that’s done with drones, which inspect areas humans can’t easily reach—such as atop Spaceship Earth in Epcot or under the water at one of the resort’s boat piers. And a tool called the Resistograph is used to check the density of wood throughout the park to alert Imagineers if there’s rot inside and a piece needs to be replaced. [Photo: Disney] More than machines While there’s a lot of engineering work that goes on at Central Shops, there’s also a surprising amount of detail touch-up. In addition to creating character heads (in a top-secret room that Disney did not allow members of our press tour to view), the facility also handles repairs to character costumes at the Florida parks. Shoes get scuffed and details torn as Mickey and Buzz Lightyear interact with visitors. The stormtroopers are also getting a glow-up as Star Wars Day (May 4) approaches. Costumes are bought here, where they’re refurbished (a process that can take a week or two). Meanwhile, horses on the Magic Kingdom’s carousel are getting a touch
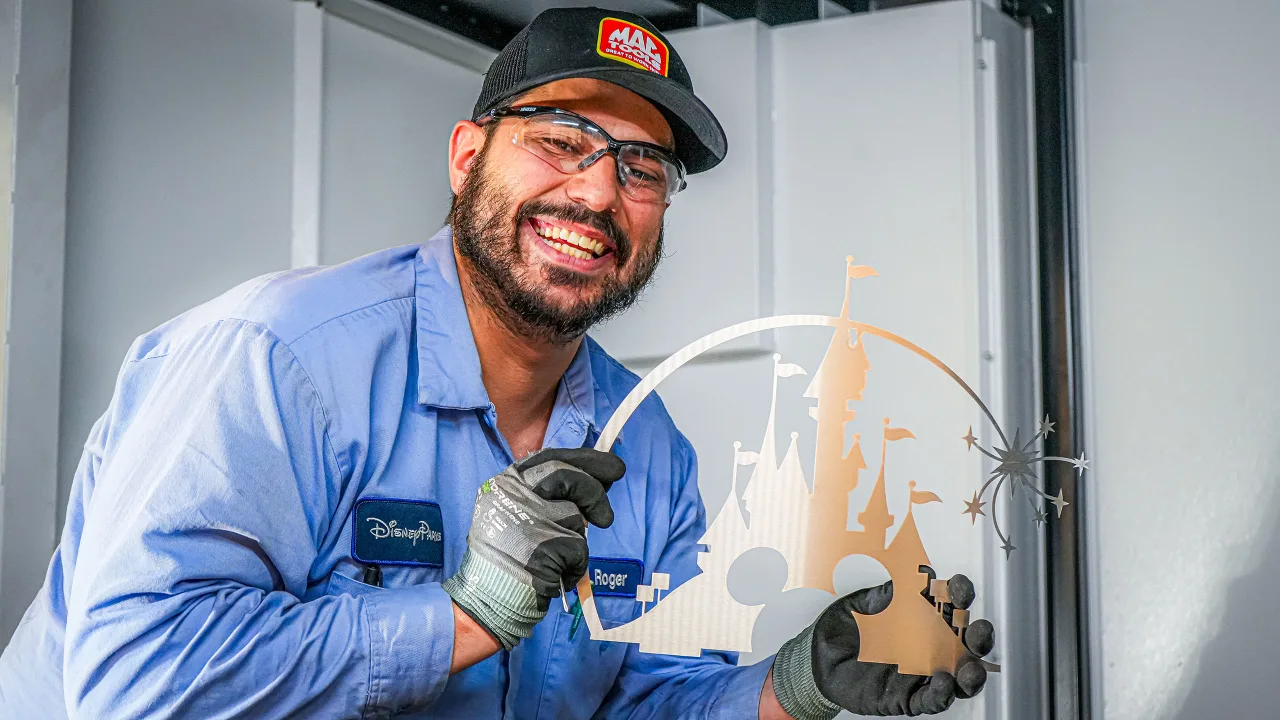
Roughly half a mile behind the Seven Dwarfs Mine Train and Ariel’s Grotto in Walt Disney World sits a nondescript cement warehouse with the words “the can-do people” written on the outside. Should tourists somehow get lost in that corner, located just outside the Magic Kingdom, it’s a place they would never pay attention to. What they might never imagine, however, is that generic building is the lynchpin of the Disney experience.
Welcome to Central Shops, a rarely spoken part of Disney that’s off-limits to visitors and most of the company’s cast members (Disney’s term for its employees). It’s ground zero for Disney World’s ride safety and an essential part of park operations around the world.
With 417 employees spanning 15 trades, from electricians to carpenters to painters, Central Shops is where every ride in the four Orlando theme parks is regularly inspected to ensure they’re safe to ride. At the same time, it’s also the corner of Disney where character heads for in-park meet-and-greets and parades in all global parks are manufactured. (Put another way, every Goofy, Mickey, Minnie, and Donald you see at the parks had their noggins made here.)
Ripping apart Disney World rides
Ride inspection is, arguably, the most important job of Central Shops. Every ride vehicle in the four Orlando theme parks ends up here on a recurring basis for inspection—and it’s far from a quick one. Ride vehicles are torn apart, down to their components. Every panel, bolt, etc. is inspected individually, a process that generally takes between 12 and 18 weeks from start to finish, says Fred Cox, director of manufacturing.
For dark rides, like a Haunted Mansion Doom Buggy, a log flume from Tiana’s Bayou Adventure, or a horse on Prince Charming’s Carousel, that’s done on a calendar basis, scheduled breaks when select cars are taken out of commission and inspected. For thrill rides, like Space Mountain, it’s meter-based, meaning vehicles are taken off the line after they’ve been ridden a predetermined number of times.
On a recent press trip through Central Shops, we saw a number of rides in various states of inspection. A collection of parts on one side was barely identifiable as a ride car from Guardians of the Galaxy: Cosmic Rewind. A few steps away, a honey pot from The Many Adventure of Winnie the Pooh gleamed, following a touch-up to its fiberglass. Sitting off to the side was a disassembled teacup from the Mad Tea Party.
And scattered throughout the shop were parts of Astro Orbiter, a ride that has been completely (and temporarily) removed from the Magic Kingdom. Every 10 years, explained Rich Votava, manager of manufacturing, the bearing at the bottom of the ride (which sits atop the People Mover in Tomorrowland) needs to be replaced. Imagineers remove it completely, giving Central Shops a chance to inspect all the ride elements, from the boom arms on the decorative planets on the ride to the ride cars. (The Disney World ride is expected to be back in the park this summer, likely in May or June.)
After ride cars are dismantled, each part is carefully inspected, some under X-ray to look for microscopic cracks in the metal. Once each part has been examined and refurbished (if needed), the components of vehicles are put back together, while the shells are repainted or refreshed. Once they are reassembled, cars are then returned to the park, where they run without riders for another two weeks to ensure everything is working properly. After that, visitors begin to pile in once again. (The maintenance schedule of most ride vehicles is staggered so that rides aren’t forced to close completely, like Astro Orbiter has.)
“We break it down to the blueprints,” says Votava.
Safety inspections go beyond ride vehicles, of course. Workers from Central Shops are in the parks nightly once visitors leave to make any necessary repairs and safety inspections for rides. Sometimes, that’s done with drones, which inspect areas humans can’t easily reach—such as atop Spaceship Earth in Epcot or under the water at one of the resort’s boat piers. And a tool called the Resistograph is used to check the density of wood throughout the park to alert Imagineers if there’s rot inside and a piece needs to be replaced.
More than machines
While there’s a lot of engineering work that goes on at Central Shops, there’s also a surprising amount of detail touch-up.
In addition to creating character heads (in a top-secret room that Disney did not allow members of our press tour to view), the facility also handles repairs to character costumes at the Florida parks. Shoes get scuffed and details torn as Mickey and Buzz Lightyear interact with visitors. The stormtroopers are also getting a glow-up as Star Wars Day (May 4) approaches. Costumes are bought here, where they’re refurbished (a process that can take a week or two).
Meanwhile, horses on the Magic Kingdom’s carousel are getting a touch-up. They have a lot of sentimental value, as they were purchased by Walt Disney himself, so the hand-carved maple stallions are treated with an especially delicate touch, with touch-ups done by artists and old layers of paint carefully sanded off so as to not hurt the detail of the carving.
Some small elements that guests might not even notice are handled in Central Shops as well, such as adding details like the small trunk hairs on a baby elephant from The Jungle Cruise, which have to be inserted one at a time by hand.
It’s detail-oriented work that’s done well out of view, so guests can stay in the Disney bubble. But with more than 115 attractions at the parks (along with more than 50 character experiences), Central Shops is essential to keeping the rides running smoothly and maintaining the parks’ reputation as the so-called “happiest place on earth.”